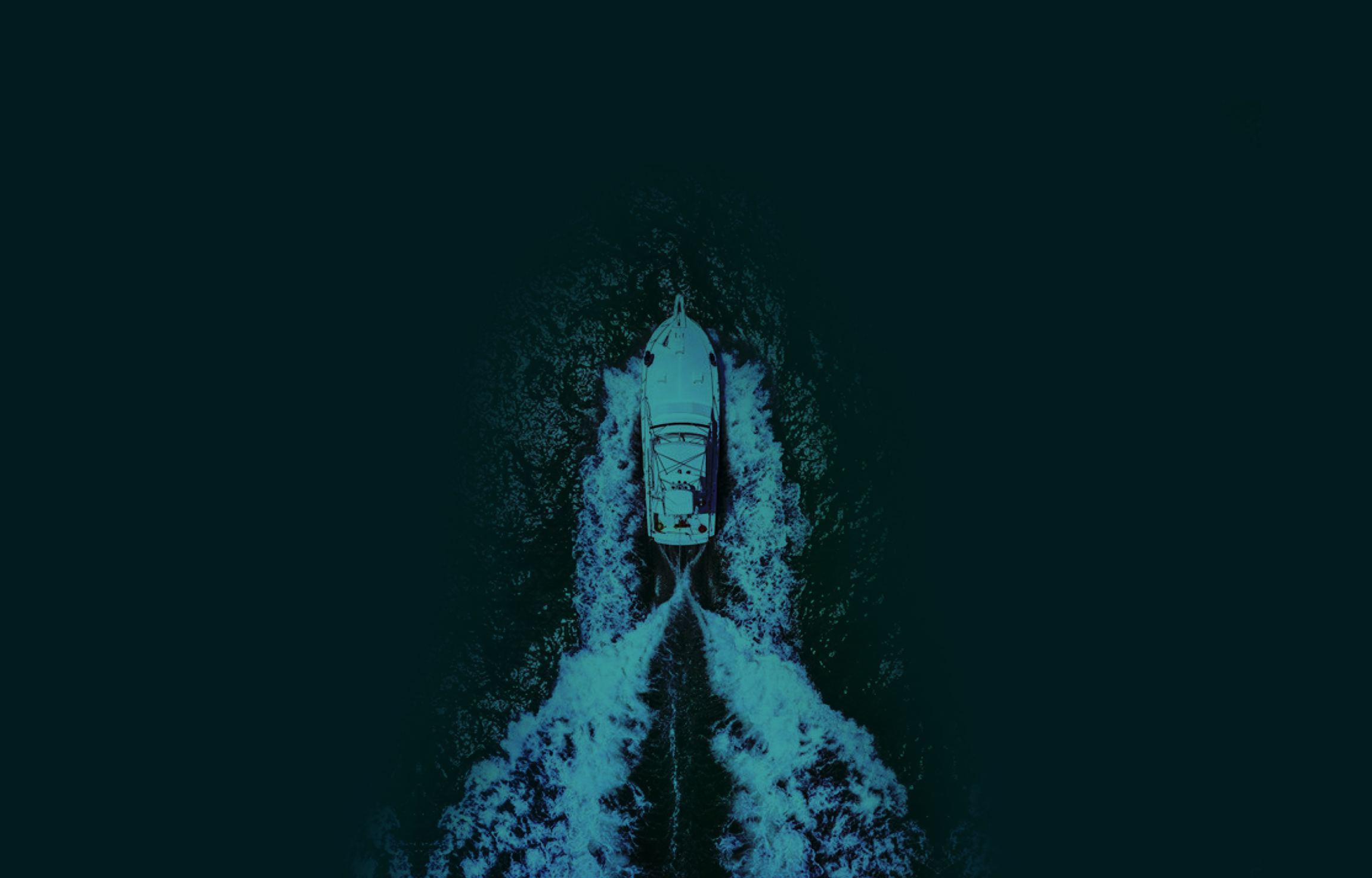
Wilmington NC’s Premiere
Volvo Penta and Yanmar Specialists
910-620-3212
Serving the Needs of a Thriving Community
Southeast North Carolina is one of the fastest growing areas in the country and the marine business is no exception. From warranty work on brand new Azimuts to getting a trawler back on her way up the Great Loop, decades of experience allow us to provide professional, prompt and unrivaled service.
Our Organization
With over 20 years of experience in the marine diesel industry, Specialized Mechanical Services is a recognized leader in the greater Wilmington, NC region. SMS offers repair and maintenance services on inboard marine diesel engines, specializing with both Volvo Penta and Yanmar engines. We are also a provider of quality diesel marine parts.
and Maintenance
Repair, Service
Whether Wilmington and the surrounding areas are your port of call, or you are just cruising through the Coastal Carolinas, if you need emergency repair/service or just routine maintenance to help you get underway, please contact our service manager Kris Ward at:
910-620-3212 Ext. 4
Parts Department
Along with Volvo Penta and Yanmar, SMS also provides quality marine diesel parts from a wide variety of manufacturers including Depco, Westerbeke, Paxton, and many others.
For parts inquiries, please contact Lee McLaughlin at:
parts@specializedmechanical.com
or give him a call at: